Diamondback Hopper
The Diamondback Hopper uses patented one-dimensional convergence dynamics to ensure smooth material flow without the need for moving parts. It eliminates issues like arching, ratholing, flooding, and erratic flow, while also enhancing process flow rates.
Standard Diamondback Hoppers
These hoppers feature innovative one-dimensional convergence dynamics that prevent arching and ratholing. They often replace the need for additional equipment such as vibrators, air cannons, and expensive mass-flow screw feeders. This results in uniform mass flow without maintenance, leading to increased production rates and minimized downtime.
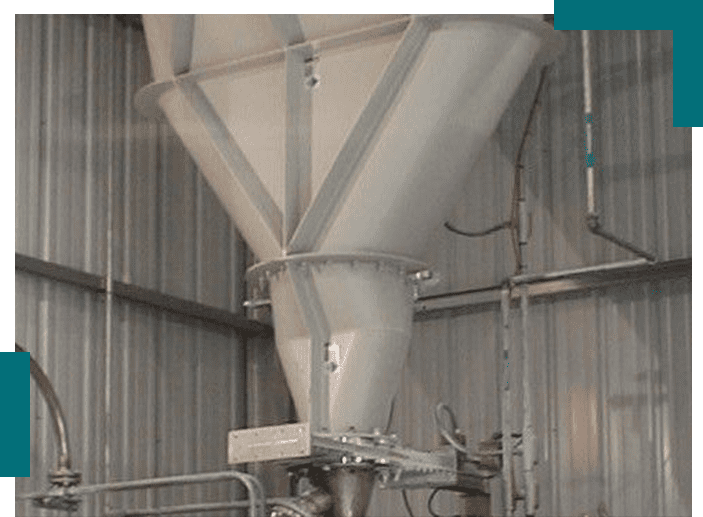
Milling Hopper Case History: Cereal Producer
A Californian milling company faced challenges with stable minds ratholing and excessive dust during truck loading. To resolve this, they replaced the existing vibrated hopper with three Arch-breaking Diamondback Hoppers equipped with air permeation.
Installation involved careful coordination, including jackhammering and cleaning. Once operational, dust during loading was significantly reduced, and with the air permeation unit, trucks loaded in a fraction of the time. The success was evident in the installation of a second identical bin.
Coal Industry Diamondback Hopper
Converts four-foot diameter outlets to two-foot-diameter outlets.
Retrofit Applications
Multiple Outlet Power Plant Bunkers
Single Outlet Bunkers
Bottom Tunnel Reclaim Hoppers for Coal
Truck Dump Hoppers
Rail Dump Hoppers
Dozer-Loaded Reclaim Points
New Construction for Hangup-Free Operation
Key Features
Constructed with stainless steel for corrosion and wear resistance
Standard pre-engineered designs for various applications
Two-foot-diameter outlets as standard
Transitions to circular bins with a predrilled extra flange
Custom transitions to square or rectangular hoppers at structurally optimal positions
Shipped in sections for on-site bolted assembly
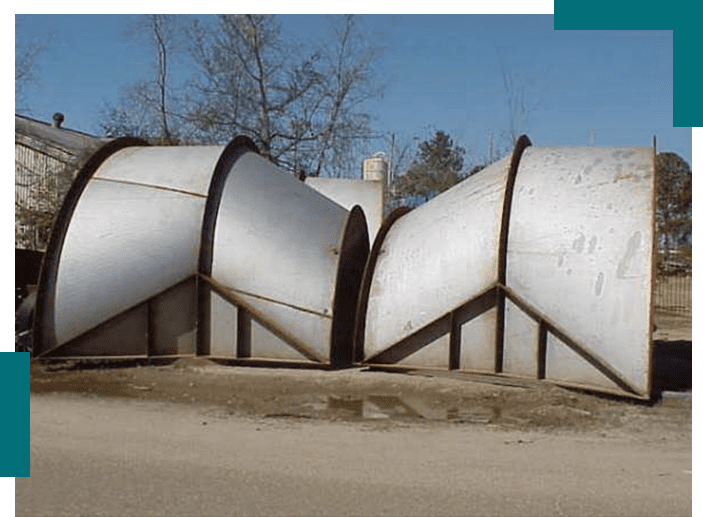
Coal Hopper Case History: Public Utility Company
Faced with the U.S. Government's mandate for cleaner power generation, a Midwestern utility adopted Powder River Basin (PRB) coal from Wyoming. Despite its cleaner-burning nature, PRB coal caused issues in the utility's pyramid-shaped hoppers, necessitating a solution.
After extensive testing, the utility chose to retrofit its existing hoppers with Diamondback Hoppers. The unique racetrack configuration of the Diamondback Hopper optimizes energy conservation, achieving smoother flow compared to traditional conical hoppers.
The modular nature of Diamondback Hoppers allowed seamless retrofitting, accommodating varying shapes and headroom constraints. The result was a multiple-outlet coal bunker operating flawlessly, solving the problem at a fraction of the cost of standard hopper designs.
Pharmaceuticals
An important requirement in the manufacture of tablets and capsule filling is the assay of active ingredients in the lot. Typical steep conical hoppers can cause rejects due to segregation of the batch during discharge. Archbreaking Diamondback hoppers eliminate this problem by delivering the batch contents in a First-In-First-Out (FIFO) flow pattern.
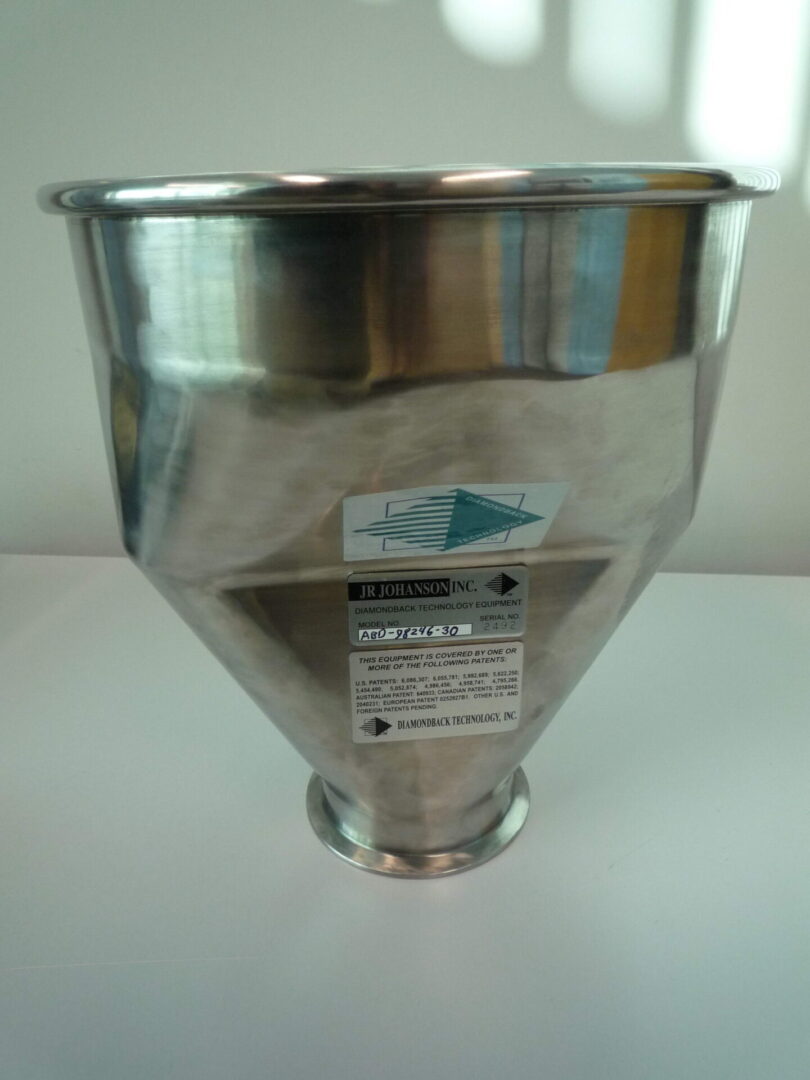